zorrex
Enjoys the Abuse
So I have been nonexistent the past couple weeks and especially the past couple days. My soul has been CONSUMED the past couple weeks with Steel Bridge! Basically, we have a team to design, fabricate, and competitively construct and load a 20ft long steel bridge. There are VERY strict dimensional and construction rules.
We constructed our bridge in about 15 minutes (before penalties), and our bridge weighed 249 lbs (again, before penalties). It also held the entire load of 2500 lbs that all bridges were loaded with, and out of all the teams, performed the BEST. It had an aggregate deflection of 5/8". The aggregate deflection was the measure of all the deflections at 3 points after the first grate was loaded and after the second grate was loaded (see pics). After the first grate was loaded, the center of the bridge actual went UP instead of sagging, meaning we had a NEGATIVE deflection! Our bridge's aggregate deflection beat out second-best MIT's bridge
.
Unfortunately, we had a dimensional violation which caused out team to fall into 4th place overall. The scoring is based on your construction time, your bridge weight, and your deflection. If we didn't have a dimensional violation (we found out later we could have avoided said dimensional violation, UGH), our team would have placed 2nd overall to MIT, and we would have gone to Las Vegas for the national competition
.
Oh well, we still had the BEST BRIDGE! Pics to follow...
The build team...
Most of the team standing on the bridge after our extremely successful loading!
Me being an idiot before/while loading the bridge
Getting ready to load the bridge...
FULLY LOADED to 2500 lbs! Notice how it's as straight as heck!
Co-captain Bill leaping over the bridge during construction...
Construction...
More construction...
We constructed our bridge in about 15 minutes (before penalties), and our bridge weighed 249 lbs (again, before penalties). It also held the entire load of 2500 lbs that all bridges were loaded with, and out of all the teams, performed the BEST. It had an aggregate deflection of 5/8". The aggregate deflection was the measure of all the deflections at 3 points after the first grate was loaded and after the second grate was loaded (see pics). After the first grate was loaded, the center of the bridge actual went UP instead of sagging, meaning we had a NEGATIVE deflection! Our bridge's aggregate deflection beat out second-best MIT's bridge
Unfortunately, we had a dimensional violation which caused out team to fall into 4th place overall. The scoring is based on your construction time, your bridge weight, and your deflection. If we didn't have a dimensional violation (we found out later we could have avoided said dimensional violation, UGH), our team would have placed 2nd overall to MIT, and we would have gone to Las Vegas for the national competition
Oh well, we still had the BEST BRIDGE! Pics to follow...
The build team...
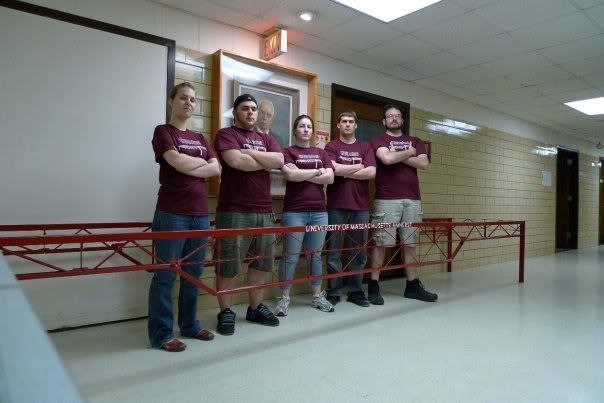
Most of the team standing on the bridge after our extremely successful loading!
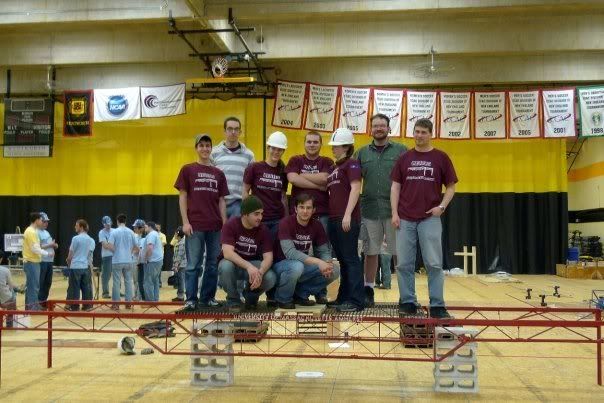
Me being an idiot before/while loading the bridge
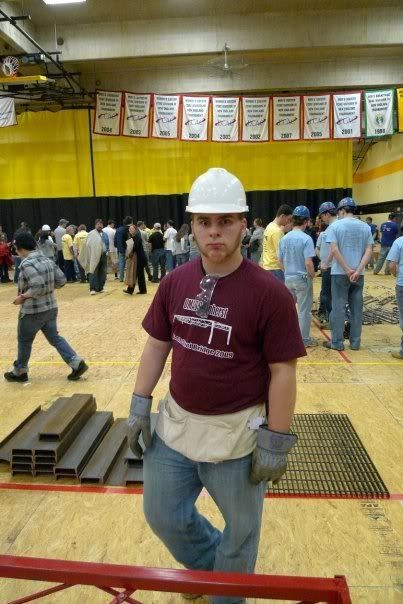
Getting ready to load the bridge...
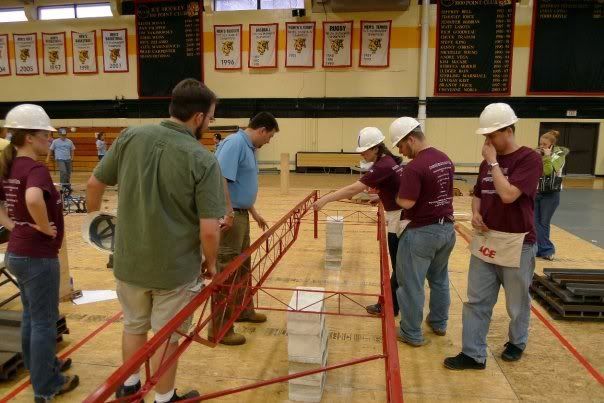
FULLY LOADED to 2500 lbs! Notice how it's as straight as heck!
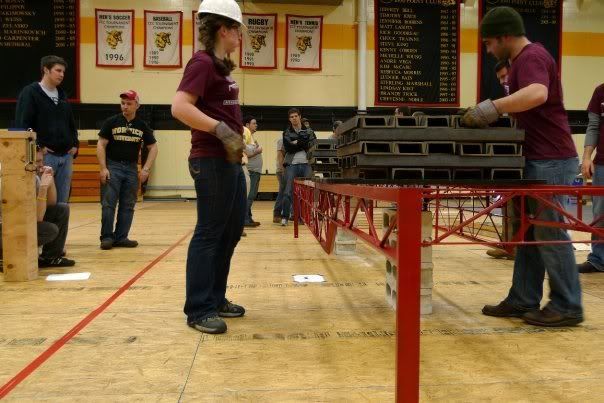
Co-captain Bill leaping over the bridge during construction...
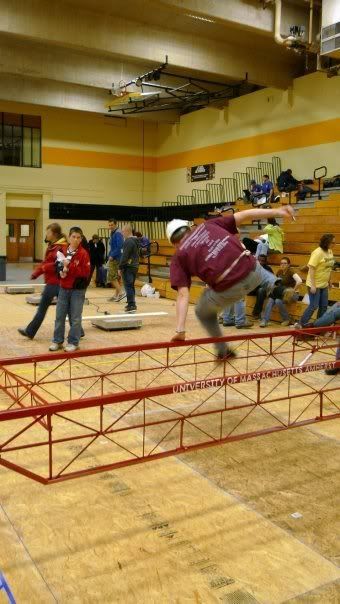
Construction...
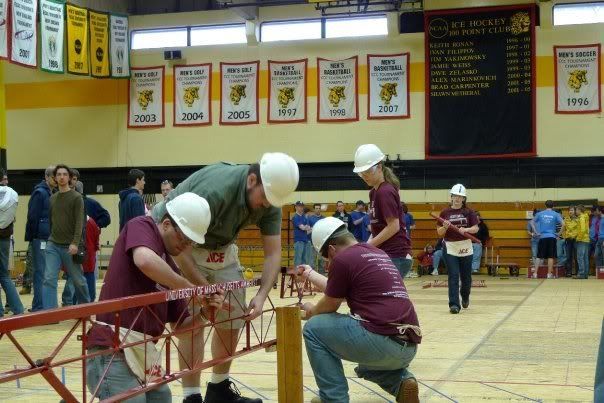
More construction...
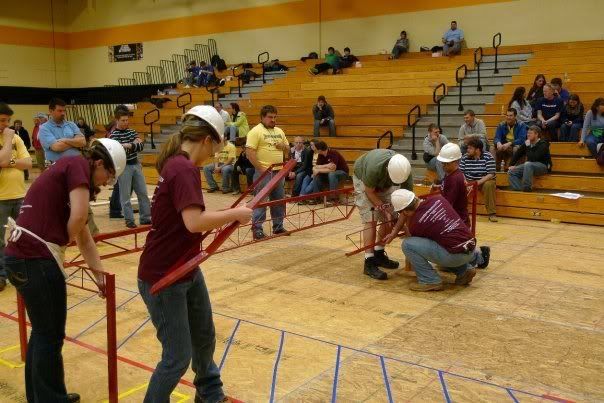