Mark T
CEG'er
As the title says really one of my tubular rear control arms has sheared at the rose jointed end link. I had a scary 5 minutes in it & it was just lucky I was only doing 20mph as if I was going faster it would have been a different story. Here's a few pics
Rearf wheel steer Mondeo, lol
I went out yesterday & put the old arms back on now so I've just got to get the tracking redone & all should be OK again.
Looking at the where it's sheared the rose joint on the end has seized solid, so is the other side, so I think this is why the threaded bit, where the rose jointed end link goes into the arm, has sheared.
These were fitted last October & the car has done just under 8000 miles with them on. I don't drive the car that hard & I was greasing the arms up every 2000 or so miles so it looks like the good old British weather has taken it's toll on mine & they needed to be greased more often than that. Oh well doesn't matter as they are off now.
I'm going to look into getting a replacement end link for it & then decide to either sell the arms or put them back on & grease them more often but I expect I'll be selling them as I'm not sure I can be bothered to get out there & grease them all the time.
Sheared end link stuck in bar
Sheared end link
Has anyone else heard of this?
Rearf wheel steer Mondeo, lol
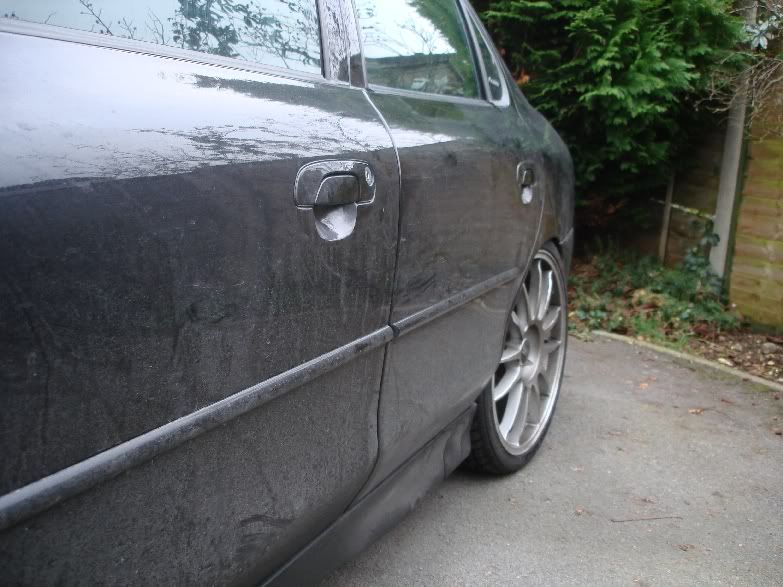

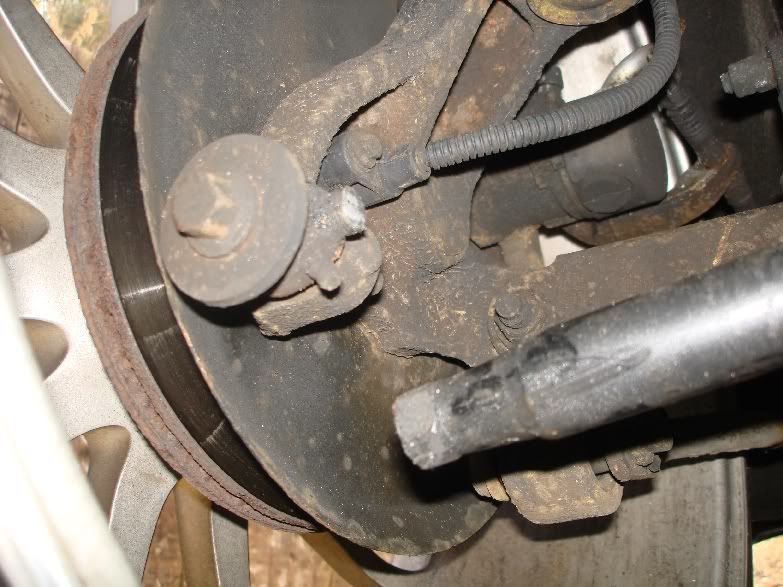
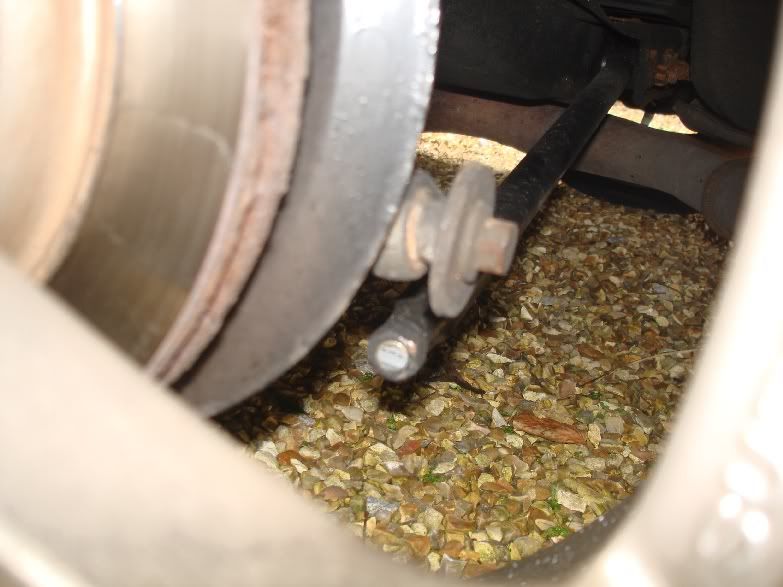
I went out yesterday & put the old arms back on now so I've just got to get the tracking redone & all should be OK again.
Looking at the where it's sheared the rose joint on the end has seized solid, so is the other side, so I think this is why the threaded bit, where the rose jointed end link goes into the arm, has sheared.
These were fitted last October & the car has done just under 8000 miles with them on. I don't drive the car that hard & I was greasing the arms up every 2000 or so miles so it looks like the good old British weather has taken it's toll on mine & they needed to be greased more often than that. Oh well doesn't matter as they are off now.
I'm going to look into getting a replacement end link for it & then decide to either sell the arms or put them back on & grease them more often but I expect I'll be selling them as I'm not sure I can be bothered to get out there & grease them all the time.
Sheared end link stuck in bar
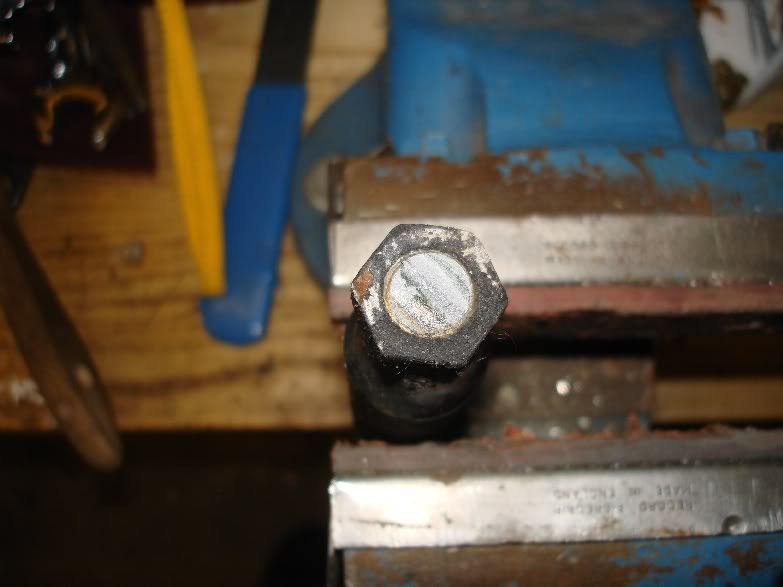
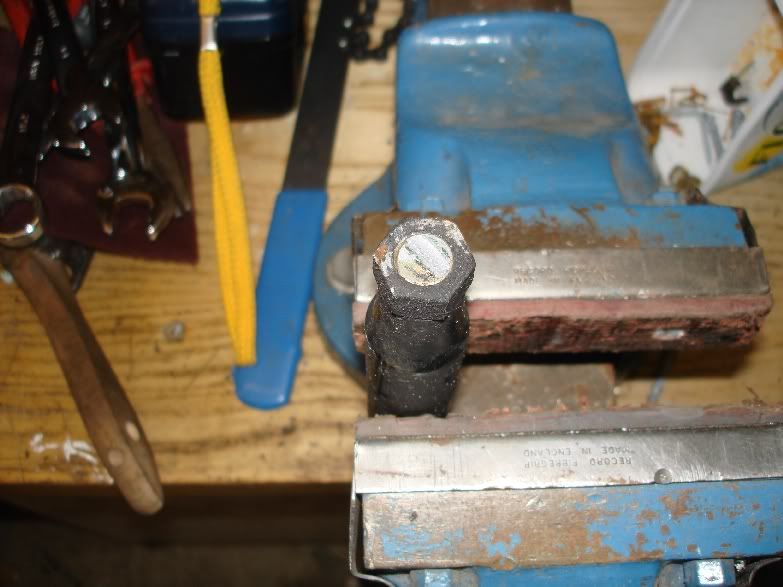
Sheared end link
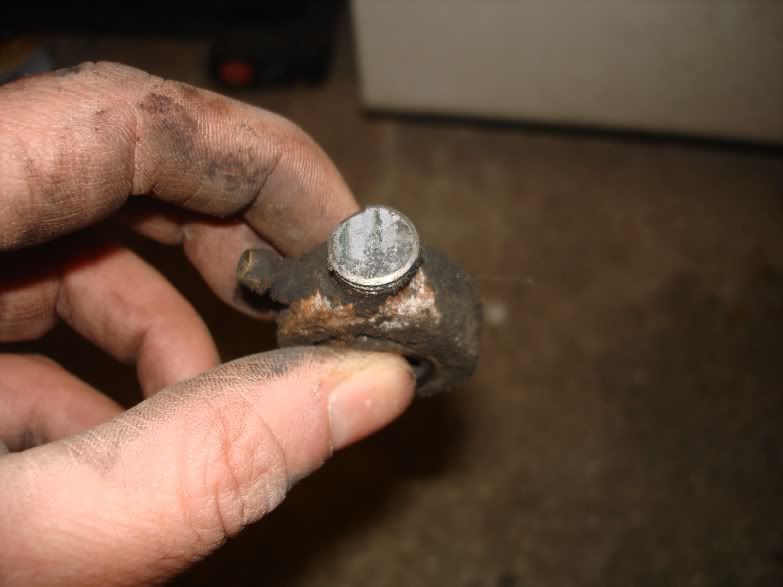
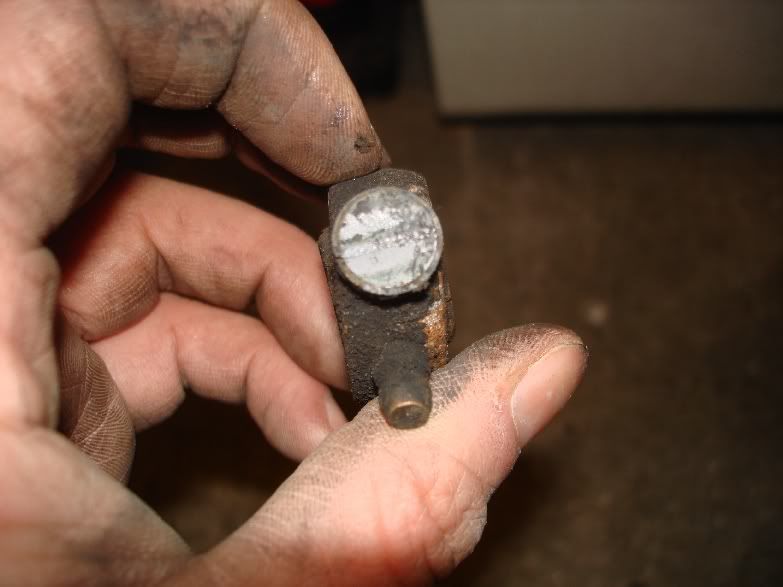
Has anyone else heard of this?