CrazyTalkSVT
Veteran CEG'er
Just curious who might be on board for a set of the Rear Lateral Toe Bars like I built for my car. The price would be $250.00 + shipping costs for bars just like the ones I made for my car.
If you wanted to upgrade to Delrin Bushings, the price would increase to $285.00 + shipping.
If you want to upgrade to Military Grade Heim joints, the price increases to $635.00 + shipping.
So for Military Grade Heims along with Delrin Bushings the price is $670.00 + shipping.
If you're only interest is in Delrin Bushings, we machine them to size and price accordingly. Typically, the cost is roughly $30.00 for the Delrin to complete one endlink, but there is an additional cost for the inner sleeve which depends on the size bolt for your application.
Here is a copy/paste of the OP:
I'll show you what I did for the rear lateral bars. The bars are 1" DOM 3/16" wall. The spindle side is tapped 3/4 - 16 for the heim. I used a 3/4" hole and shank sized heim that is PTFE(Self lubricating teflon) lined. The inner end link was 2" DOM with a 3/8" wall that has been bored for an interference fit for the factory bushings.
Because the heim is a 3/4" hole which is obviously too big, but the housing itself is physically smaller than factory I made spacers to take up the difference. They get the bolt size back down to the metric factory size as well as take up .25" to align the bar back to straight.
From the factory Ford uses eccentric washers and slotted holes on the inner mounts for toe in and toe out adjustments. Now the adjustment is on the spindle side using the heims threads, but those pesky slotted holes are still on the subframe. So the four machined .25" thick washers you see in the pictures are what align the inner end link to center. So now the chance of the bar slipping in the slotted hole is gone.
If you wanted to upgrade to Delrin Bushings, the price would increase to $285.00 + shipping.
If you want to upgrade to Military Grade Heim joints, the price increases to $635.00 + shipping.
So for Military Grade Heims along with Delrin Bushings the price is $670.00 + shipping.
If you're only interest is in Delrin Bushings, we machine them to size and price accordingly. Typically, the cost is roughly $30.00 for the Delrin to complete one endlink, but there is an additional cost for the inner sleeve which depends on the size bolt for your application.
Here is a copy/paste of the OP:
I'll show you what I did for the rear lateral bars. The bars are 1" DOM 3/16" wall. The spindle side is tapped 3/4 - 16 for the heim. I used a 3/4" hole and shank sized heim that is PTFE(Self lubricating teflon) lined. The inner end link was 2" DOM with a 3/8" wall that has been bored for an interference fit for the factory bushings.
Because the heim is a 3/4" hole which is obviously too big, but the housing itself is physically smaller than factory I made spacers to take up the difference. They get the bolt size back down to the metric factory size as well as take up .25" to align the bar back to straight.
From the factory Ford uses eccentric washers and slotted holes on the inner mounts for toe in and toe out adjustments. Now the adjustment is on the spindle side using the heims threads, but those pesky slotted holes are still on the subframe. So the four machined .25" thick washers you see in the pictures are what align the inner end link to center. So now the chance of the bar slipping in the slotted hole is gone.
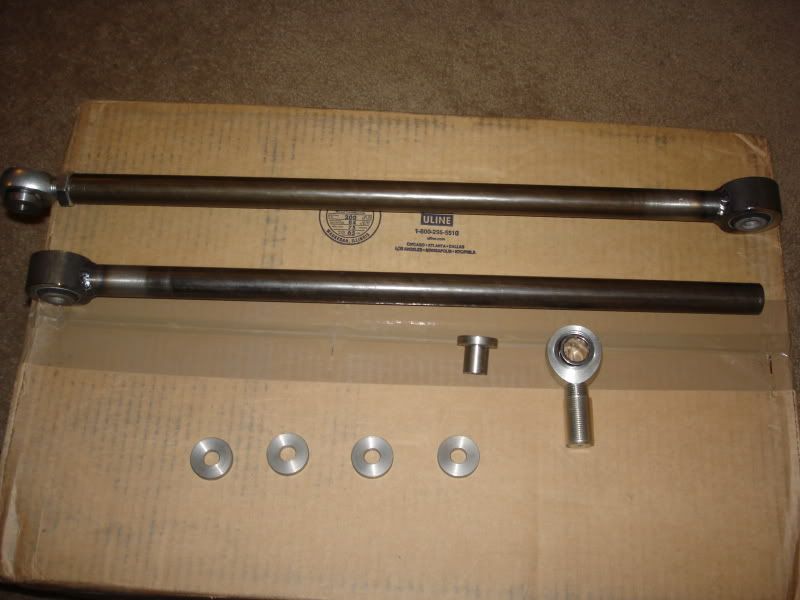
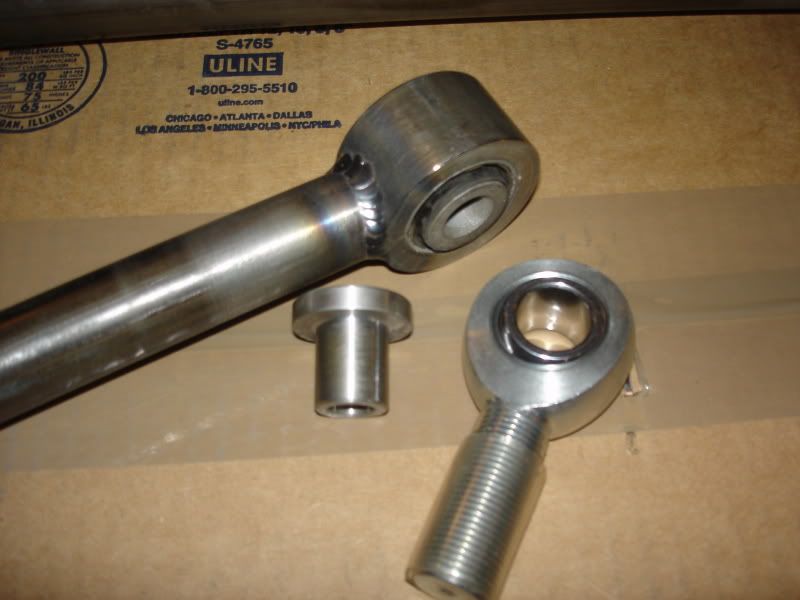
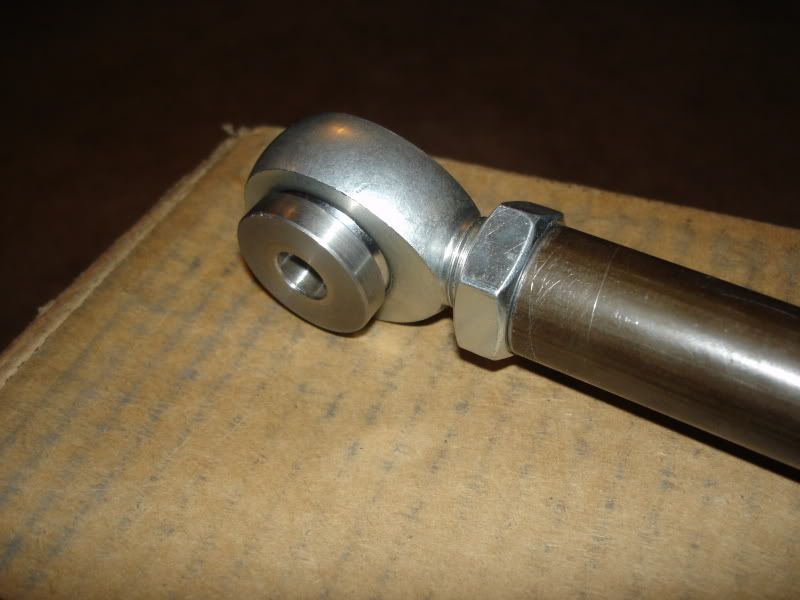