Here are the pics of one of my heads,, both are finished and looking good,, the main reason i am posting is mainly to brag,, i am not going to be using any epoxy in the injector valleys left over from the original setup. Bugzuki, one of the members on the board is making steel plates that cover the valleys, so you would never have to worry about epoxy or JB Weld falling down into your heads. You would silicone the plate to the head, and be able to use the stock lower intake gasket. But Bugzuki is working on a gasket to go under the plates,,,, the plates in the pics are not the ones that cover the valleys,(but are earlier designs of the same product) i will be receiving those next week and will post pics of the how i did it for anyone who is interested in getting some of these,, I think this is a great product. the possibility of epoxy falling into the engine at any time was very frightening to me and actually was the main reason i wanted to go hybrid cause at least the epoxy involved in that would just fall in the crankcase if it went sour. but now i am happy as hell.
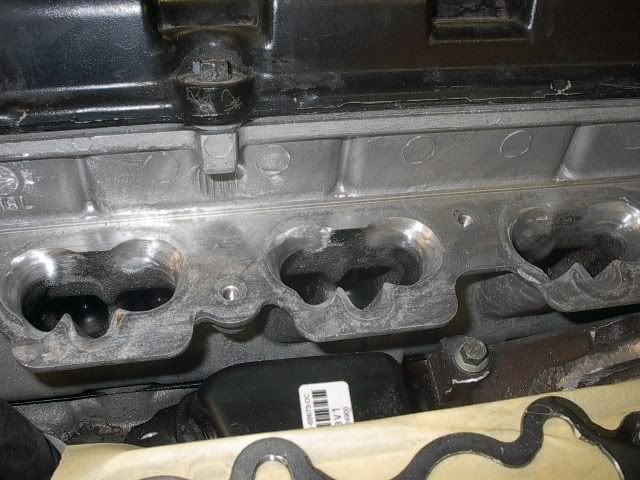
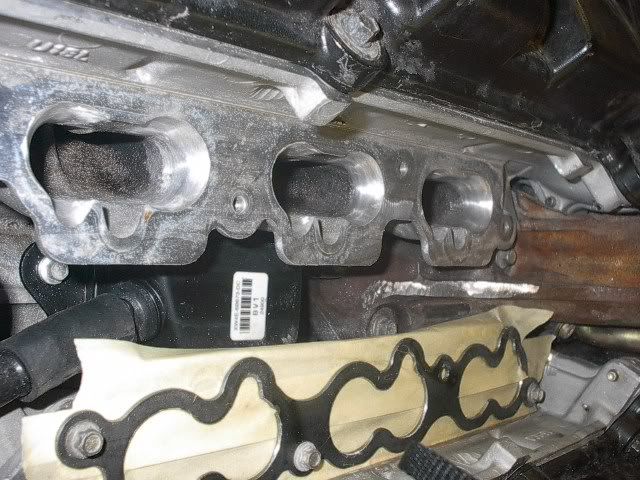