ButtonPuncher
Veteran CEG'er
Hi,
I built this a few years ago. On my original '96 Contour, the halfshafts were totally rusted to the hubs. I had to take the hubs, axels and all to a machine shop to have them pressed out. It was a royal pain and it cost a chunk of change.
If you want to build one, you need the following...
Two old rotors
5/8" drill bit
Four 18" pieces of 5/8" threaded rod
Sixteen 5/8" nuts
Sixteen 5/8" washers
Eight 5/8" lock washers
20 ton bottle jack. I got mine from Northern Tool.
It cost about $75 total to build.
You need to use a drill press to drill the rotors. Carefully draw an X pattern on the rotor. Measure so that the holes are 6" apart. After you've drilled the holes, put the two inside nuts on each piece of threaded rod. Spin the nuts onto the threaded rod about 2". Now this part is critical... Lay the pieces of threaded rod down onto a table side-by-side. Adjust all of the nuts so that they are exactly the same distance apart on each piece of threaded rod. Next put a washer on each end and feed it through the rotor. Be sure not to turn the nuts, if you do it will screw up the length. Carefully put on the outside washer, lock washer, and nut. Try to tighten the outside nut while holding the inside nut stationary. Once they are all tightened up, set the whole assembly on end on your table. (It looks like some kind of badass trophy. LOL!) Next, set the jack inside. Put a few wire ties end-to-end so that you have enough length to go around the body of the jack then around one of the threaded rods. Use two of these around the base of the jack and two around the top of the jack. That's it! You're done!
Because of the incredible forces involved, I used four pieces of 5/8" threaded rod. Like I said above, the length of the rods are critical. You want to adjust the inside nuts so that they are all exactly the same length. If they aren't, the shorter rod will take all of the force and break. You may also think that a 20 ton jack is insane overkill. It's not. I was using a 6 ton bottle jack and it worked for a couple projects. On the '96 MTX that I'm working on right now, the 6 ton didn't budge the halfshaft. That's 12,000lbs of force! And it didn't move!!! I got the 20 ton jack and that was able to break the halfshaft loose. Each of those pieces of threaded rod is handling 10,000lbs of force. 40,00lbs total.
A couple readers right now are probably thinking, "Why didn't you use smaller rod? The wheel studs are taking all of that force and are much smaller!" True, the wheel studs are smaller. BUT they are also high-grade bolts with a very high tensile strength. The hardware store threaded rod isn't heat treated. Plus because of the length of the rods, they will be prone to stretching. I had actually thought about using 3/4" threaded rod but settled on 5/8".
Check it out!!!
I used wire ties to hold the jack between the rods.
Just put the jug nuts on backwards with a washer to bolt it to the hub...
Lined up and ready to go.
Make sure that the jack is centered on the halfshaft.
Don't go too far. I stopped when the jack was about even with the raised lip of the hub. For the rest of the way, use a gear puller to shove the halfshaft throught and out the back of the hub.
Heres' the 6 ton jack that wasn't powerful enough.
HTH,
BP
I built this a few years ago. On my original '96 Contour, the halfshafts were totally rusted to the hubs. I had to take the hubs, axels and all to a machine shop to have them pressed out. It was a royal pain and it cost a chunk of change.
If you want to build one, you need the following...
Two old rotors
5/8" drill bit
Four 18" pieces of 5/8" threaded rod
Sixteen 5/8" nuts
Sixteen 5/8" washers
Eight 5/8" lock washers
20 ton bottle jack. I got mine from Northern Tool.
It cost about $75 total to build.
You need to use a drill press to drill the rotors. Carefully draw an X pattern on the rotor. Measure so that the holes are 6" apart. After you've drilled the holes, put the two inside nuts on each piece of threaded rod. Spin the nuts onto the threaded rod about 2". Now this part is critical... Lay the pieces of threaded rod down onto a table side-by-side. Adjust all of the nuts so that they are exactly the same distance apart on each piece of threaded rod. Next put a washer on each end and feed it through the rotor. Be sure not to turn the nuts, if you do it will screw up the length. Carefully put on the outside washer, lock washer, and nut. Try to tighten the outside nut while holding the inside nut stationary. Once they are all tightened up, set the whole assembly on end on your table. (It looks like some kind of badass trophy. LOL!) Next, set the jack inside. Put a few wire ties end-to-end so that you have enough length to go around the body of the jack then around one of the threaded rods. Use two of these around the base of the jack and two around the top of the jack. That's it! You're done!
Because of the incredible forces involved, I used four pieces of 5/8" threaded rod. Like I said above, the length of the rods are critical. You want to adjust the inside nuts so that they are all exactly the same length. If they aren't, the shorter rod will take all of the force and break. You may also think that a 20 ton jack is insane overkill. It's not. I was using a 6 ton bottle jack and it worked for a couple projects. On the '96 MTX that I'm working on right now, the 6 ton didn't budge the halfshaft. That's 12,000lbs of force! And it didn't move!!! I got the 20 ton jack and that was able to break the halfshaft loose. Each of those pieces of threaded rod is handling 10,000lbs of force. 40,00lbs total.
A couple readers right now are probably thinking, "Why didn't you use smaller rod? The wheel studs are taking all of that force and are much smaller!" True, the wheel studs are smaller. BUT they are also high-grade bolts with a very high tensile strength. The hardware store threaded rod isn't heat treated. Plus because of the length of the rods, they will be prone to stretching. I had actually thought about using 3/4" threaded rod but settled on 5/8".
Check it out!!!
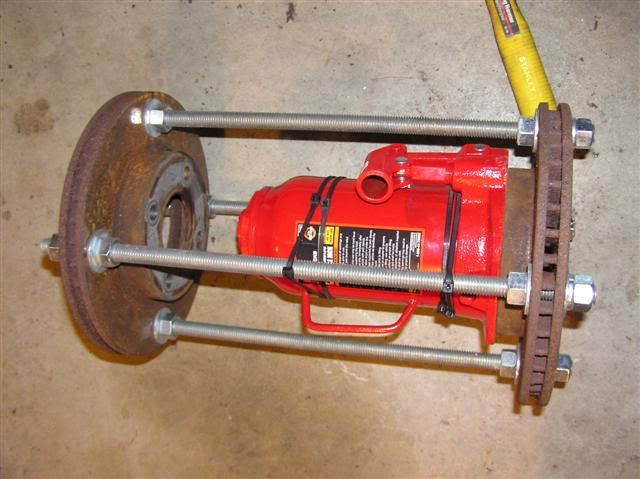
I used wire ties to hold the jack between the rods.
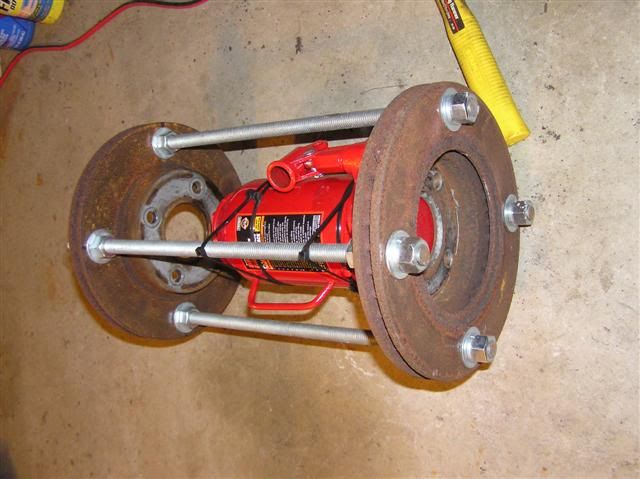
Just put the jug nuts on backwards with a washer to bolt it to the hub...
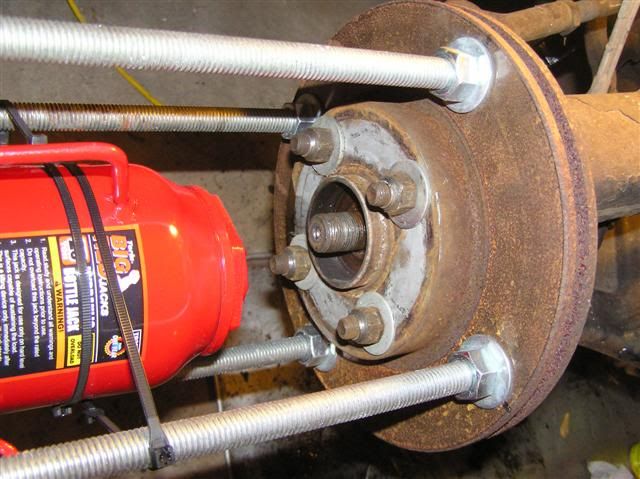
Lined up and ready to go.
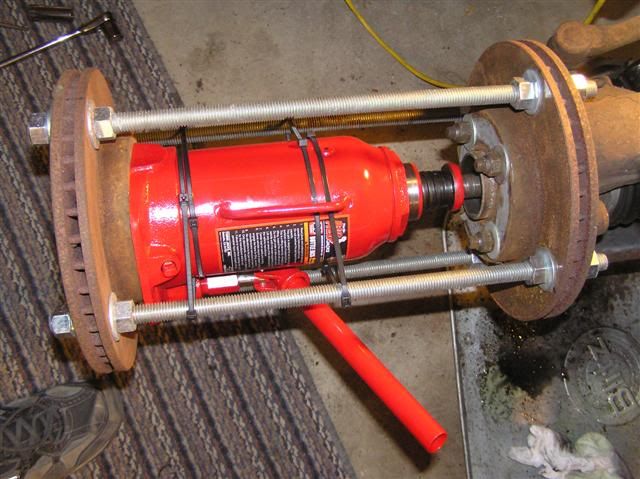
Make sure that the jack is centered on the halfshaft.
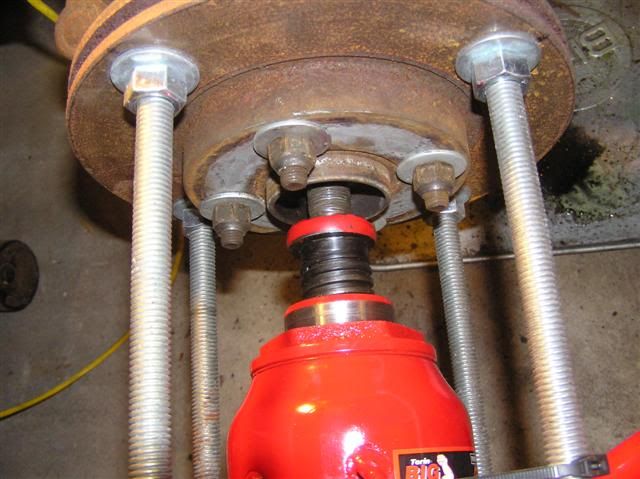
Don't go too far. I stopped when the jack was about even with the raised lip of the hub. For the rest of the way, use a gear puller to shove the halfshaft throught and out the back of the hub.
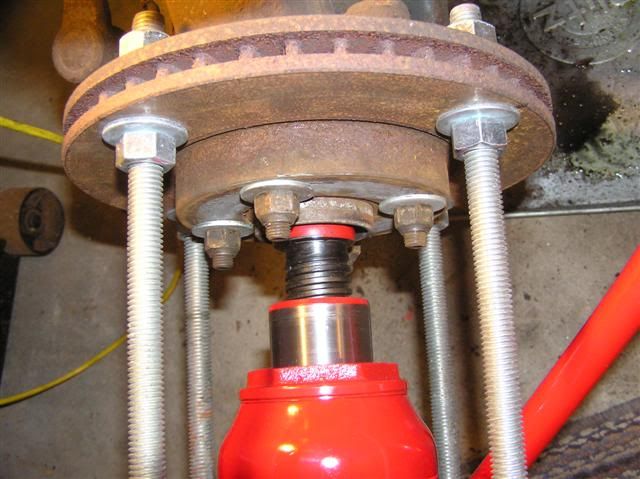
Heres' the 6 ton jack that wasn't powerful enough.
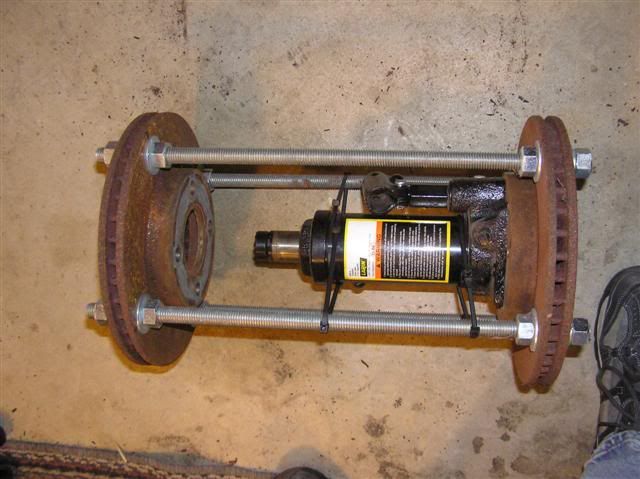
HTH,
BP